Как правильно определить размер сварного шва: советы экспертов и практиков
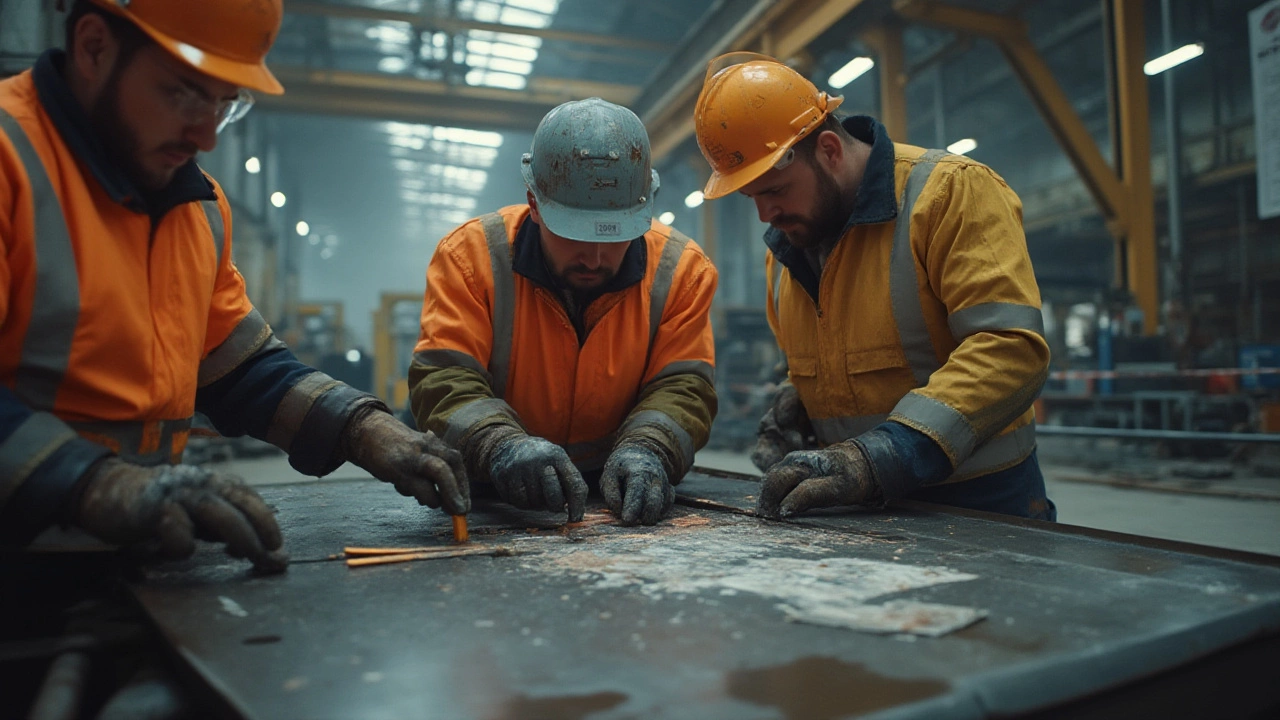
Самый неожиданный способ узнать, что сварочный шов сделан неправильно? Посчитать деньги на ремонт. Сварка — не область для лотереи: если не знаешь, как задать правильный размер, результаты могут быть печальными и дорогими. Для кого-то это просто полоска металла, а для опытного сварщика — почти личная подпись, гарантия, что вся конструкция не превратится в груду хлама при первой нагрузке. Здесь важен не только внешний вид, но и цифры: точный размер шва может спасти от деформаций, разлома или, например, утечки в резервуаре с водой или газом.
Размер сварного шва нельзя определять «на глаз». Вы удивитесь, но в России ежегодно около четверти аварий на промышленных объектах происходят из-за неверной геометрии и размеров швов. ГОСТы написаны не потому, что инженеры не знают, чем заняться, а чтобы каждый сварщик чётко понимал: излишки металла — не признак надёжности, как и экономия на ширине шва.
Почему все так на этом зациклены? Всё просто: чем точнее ты знаешь, сколько металла и где положить, тем выше прочность соединения, срок службы и минимальный риск возникновения коррозии по краям шва. Плюс, не придётся потом мучительно переделывать работу под строгим взглядом контролёра.
Какими бывают размеры сварного шва и на что они влияют
Самая популярная ошибка среди новичков — путать ширину шва с его высотой. На деле важно и то, и другое, плюс ещё глубина проплавления, если речь о стыковых соединениях. Вот где начинается настоящая арифметика сварщика: каждый параметр отвечает за определённую прочность и несущую способность металлической конструкции.
Классика для России — профильный сварной шов по ГОСТ 5264-80. Тут сразу всё прописано до миллиметра: высота усиления, ширина шва, даже минимально допустимая глубина проплавления. Для угловых швов ширина полки — это главный параметр. Любой профи скажет: для простых конструкций — минимум 4 мм, а для несущих балок или емкостей под давление — иногда доходит до 10-12 мм.
Опытные инженеры знают: если переборщить с шириной, риск хрупкости только возрастает. Это связано с неравномерным охлаждением металла и скрытыми дефектами. Уже доказано исследованиями ЦНИИ конструкционных материалов, что оптимальный размер шва повышает прочность на 18–26%, по сравнению с «на глаз».
Если вы делаете многослойный шов, толщина каждого прохода тоже важна — снижается риск появления внутренних трещин. В проектной документации всегда указывается, сколько слоёв, какой размер и даже угол наклона электрода. Не стоит думать, что «чем больше, тем лучше»: современное оборудование сэкономит не только металл, но и время.
Вот реальный пример: электросварщик на строительстве мостов в 2023 году рассказывал, что уменьшение ширины углового шва всего на 1,5 мм позволило снизить затраты на материал на 4%, без потери качества.
Тип шва | Рекомендуемый размер (мм) | Требования ГОСТ |
---|---|---|
Угловой однослойный | 4 – 8 | ГОСТ 5264-80 |
Угловой многослойный | 6 – 10 | ГОСТ 8713-79 |
Стыковой с разделкой кромок | 3 – 6 | ГОСТ 14771-76 |
Стыковой без разделки | 2 – 4 | ГОСТ 16037-80 |
На практике, конечно, никто не бегает с линейкой во время сварки, большинство используют шаблоны сварщика — простые металлические «уголки» с пропилами под разные размеры полок и высоты усиления. Важно помнить: отклонение даже на 0,5 мм для ответственных узлов считается браком.
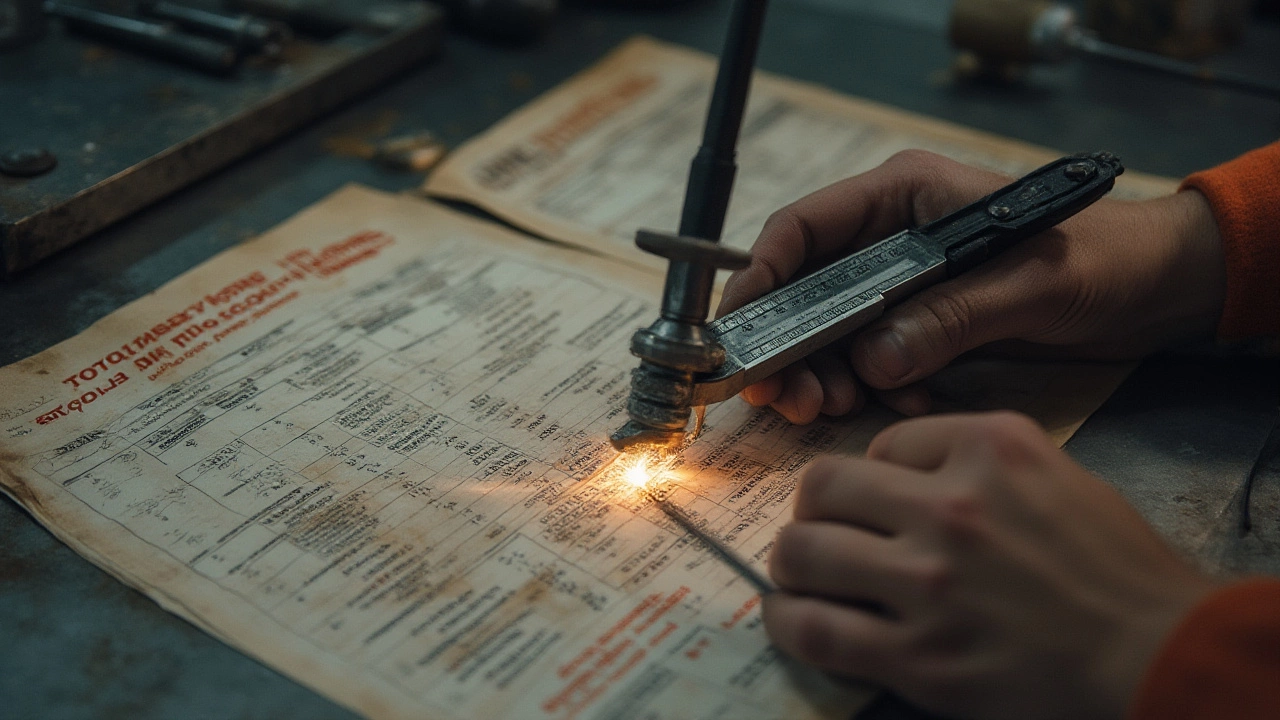
Как определить размер сварного шва на чертеже и в реальности
Любая работа начинается не с зажигания электрода, а с изучения чертежа. На чертеже часто указывается толщина металла, размер шва и вид соединения. В описании к каждому шву есть специальный символ, указывающий ширину, высоту и иногда — глубину провара. Например, если видите 6х4 — значит ширина полки 6 мм, а высота усиления — 4 мм.
ГОСТ 2.312-72 расскажет, как читать символы и обозначения на технических документах. Все размеры прописываются строго слева направо: сначала ширина, затем высота. Лишний миллиметр — уже нарушение.
Для промышленных объектов размеры определяет ОТК — отдел технического контроля, который использует не только шаблоны, но и ультразвуковые дефектоскопы. В домашних условиях все проще, но для хобби-конструкторов тоже есть советы:
- Используйте калибратор сварщика. Это недорогой инструмент с вырезами под разные размеры.
- Металлическая линейка — друг для самых простых задач, но не даст точности на сложных соединениях.
- После сварки обязательно измерьте ширину полки и высоту усиления.
- Помните о припусках: металл всегда немного подтягивается при остывании.
- Нож для снятия шлака не заменяет калибратора, но позволяет лучше увидеть реальный размер шва.
Если предстоит сварка ответственных деталей — закажите контроль ультразвуком. Почти 60% скрытых дефектов невозможно обнаружить даже опытным глазом. По статистике, каждая вторая крупная авария на заводах в России связана с ошибками определения размеров шва, а не качеством самого металла или оборудования.
Кстати, стоит помнить про температуру и влажность: в жару металл расширяется, и при застывании может «ужаться» сильнее, чем в мороз. Это часто упускают, когда работают под открытым небом.
Инженеры советуют: если сомневаетесь, увеличьте ширину шва только на треть допуска, а не на 100% — так вы не выйдете за нормативы и сэкономите металл.
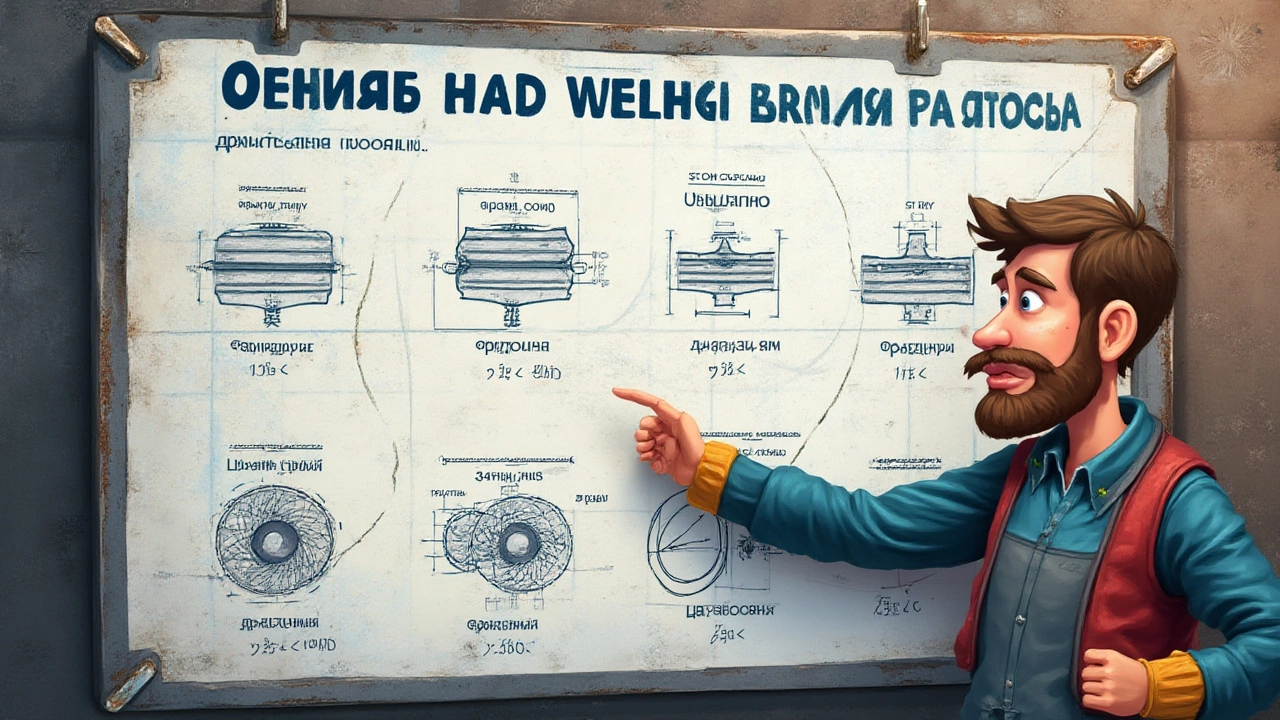
Как выбрать правильный размер сварного шва: практические рекомендации и лайфхаки
Вопрос кажется простым только на бумаге. Расчеты размеров шва — смесь математики, инженерного чутья и банального опыта. Прежде всего, помните: сварной шов не должен быть крепче металла, который соединяете — иначе вся нагрузка ляжет на «родной» металл и появится риск разлома в самом листе, а не в месте сварки.
- размер сварного шва зависит от толщины металла и типа нагрузки. Для обычных строительных конструкций можно брать за основу: ширина шва ≈ 0,7-0,8 толщины листа.
- Если конструкция будет подвижной, лучше делать более широкий, но низкий шов. Для статических соединений — наоборот, высота критичнее ширины.
- Выбирайте свойства электрода: для шва, где важна пластичность, потребуются электроды с малоуглеродистой сталью. Для прочности — с высоким содержанием легирующих добавок.
- Лучше делать пробный «сходной» шов на отдельном куске металла, чтобы убедиться в правильности настроек.
- Не гонитесь за зеркальной гладкостью — матовый, чуть бугристый шов часто крепче и устойчивее к внешнему воздействию.
Есть небольшой секрет от профи: если не можете определиться с размером, посмотрите старую схему или чертеж аналогичной конструкции. Опытные мастера всегда записывают параметры швов для разных материалов и вариантов нагрузки — это экономит время и спасает от ловушки «сделать как-нибудь».
И ещё: не стесняйтесь советоваться с инженерами-конструкторами или опытными сварщиками, если конструкция ответственная. Всё-таки, иногда чужой опыт — не роскошь, а гарантия, что шва хватит на всю жизнь конструкции.
Современные онлайн-калькуляторы размеров шва работают точнее ручных формул, попробуйте вбить туда толщину металла, углы соединения и тип шва — и тут же получите рекомендованные параметры. Но не забывайте, что даже программа не заменяет реального контроля в цеху. Проверьте штангенциркулем, калибром, и если нужно — перепроверьте ещё раз.
И не думайте, что идеальный шов возможен без ошибок: почти 12% всех сварных соединений в новом оборудовании приходится переделывать, причём именно из-за неверно выбранных размеров. Но если подойти к делу с умом, проверять и учитывать требования ГОСТ — вероятность брака минимальна. Ваш шов точно выдержит любые испытания.